Introduction
A producer of plastic containers in Germany manufactures and distributes plastic drinking cups, tableware and food trays.
A printing service is available to decorate the drinking cups. One of the machines used for this is a 6 colour VanDam cup printer. This machines was fully refurbished by GOS more than 10 years ago.
The printing process requires highly accurate colour heads: a max. of 0.02 mm deviation is allowed. If one of the heads gets less accurate, it will distort the printed image on the product.
The machine takes part in daily production, during which usually all 6 colours are required.
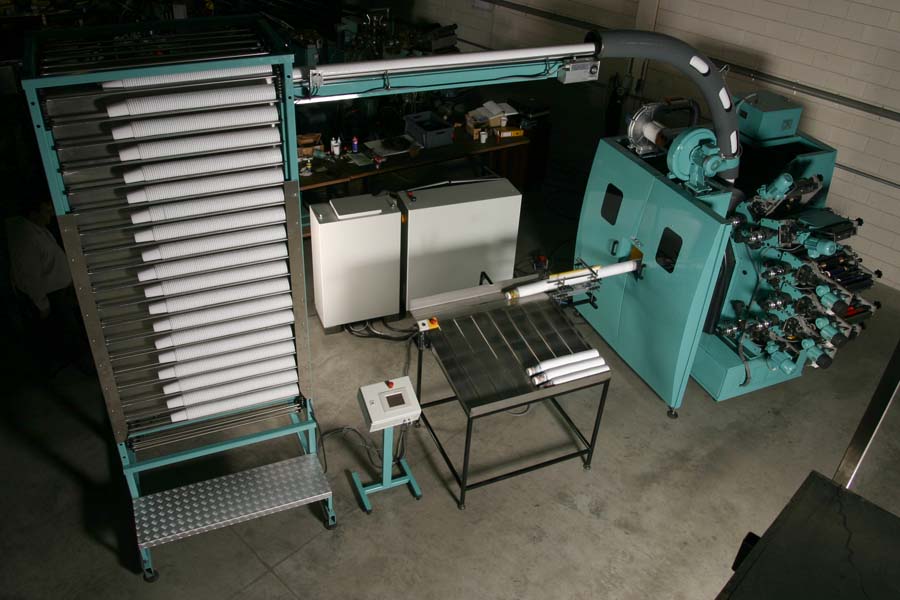
Problem
After many years of production, the color heads on this machine started to wear, decreasing the printing design’s accuracy.
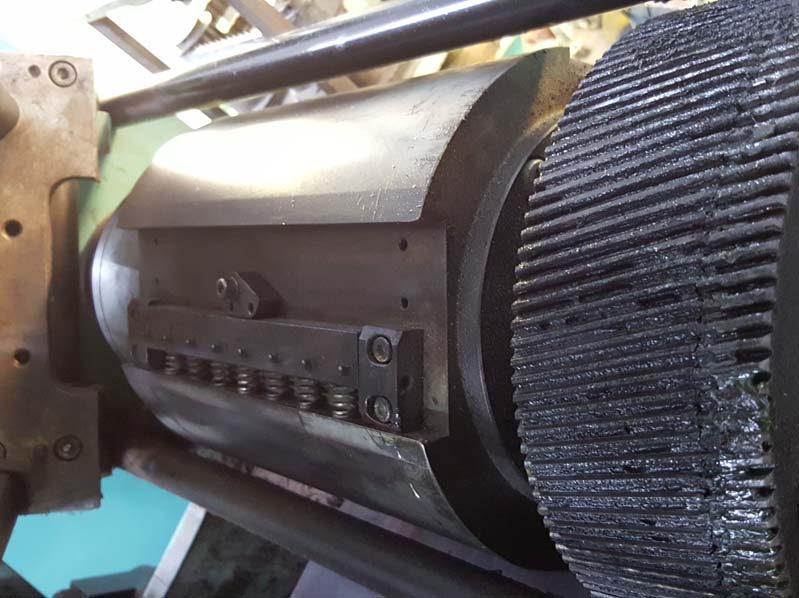
At first, regular maintenance (cleaning, lubricating, wearing parts replacement) was enough to sustain this accuracy. However, after many years of production, parts like drive gears started to wear as well. This decreased the accuracy, and forced the machine operator to adjust the machine constantly, in order to keep the required printing quality.
Without any spare colour heads available, none of the heads on the machine could be demounted for full refurbishment.
Refurbishment of all colour heads at once would result in a standstill time of around 3 months, which was not an option for the production planning.
Solution
We took a used colour head from our stock, similar to the ones on the printing machine.
During its refurbishment, this head was taken apart completely. All parts were either repaired or replaced, and then reassembled. After assembly, it was in like-new condition, and could be used as an exchange colour head.
It was exchanged with one of the colour heads on printing machine by a technical engineer from GOS in 1 day. The demounted head was taken to the GOS workshop for refurbishment.
This process was repeated until all 6 colour heads had been refurbished.

Result
After each refurbishment, the accuracy of the printed image increased. In addition, the printing machine needed less adjustment by the machine operator during production.
Next
After all 6 colour heads have been refurbished, the exchange head can be purchased from GOS. Like this, there will always be a spare head available that can be prepared as backup.
